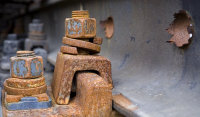
Коррозия резьбовых соединений – механизм, профилактика, удаление ржавчины
600 с лишним лет назад состоялось величайшее за всю историю Руси сражение — Куликовская битва. Десятки тысяч стрел с железными наконечниками носились в воздухе и вонзались глубоко в землю, оставаясь там навсегда. Казалось бы, в земле Куликовского поля должны были сохраниться, пусть сильно заржавевшие, остатки железного оружия. Не осталось ничего — все съела коррозия, продуктом которой является ржавчина. Прошли столетия, перепады температур и дожди сделали свое дело — ржавчина тоже исчезла, превратившись в порошок, перемешавшийся с почвой. И сейчас историки спорят — а было ли вообще сражение на Куликовом поле?
Конечно, наши обыкновенные болты и шпильки с гайками, стягивающие фланцы трубопроводов или какие-то части металлоконструкций и аппаратов, находящихся под открытым небом или в сыром помещении, не успеют у нас на глазах превратиться в труху. Зато проржавевшая гайка на ржавой шпильке может преподнести нам крайне неприятный сюрприз — оторваться вместе с частью шпильки, оставив другую часть в резьбовом отверстии. Попробуем разобраться в том, как резьбовые соединения превращаются в ржавчину.
Механизм увлажнения резьбовых соединений
Рассмотрим так называемую атмосферную коррозию стали, от которой страдают резьбовые соединения трубопроводов, машин и различных аппаратов, расположенных под открытым небом или в сырых помещениях
Основным фактором, определяющим скорость атмосферной коррозии, является степень увлажненности поверхности металла. Различают мокрую атмосферную коррозию — при наличии на металле видимой пленки воды, образующейся при относительной влажности воздуха 100% (роса, дождь); влажную атмосферную коррозию — при наличии на металле тонкой, невидимой пленки влаги, которая образуется в результате капиллярной или адсорбционной конденсации при относительной влажности воздуха ниже 100%, и сухую атмосферную коррозию — при полном отсутствии влаги на металле. Последний вид коррозии (непосредственное окисление железа кислородом воздуха) при невысоких температурах воздуха приводит к образованию на поверхности стали защитной твердой пленки оксида железа и практически не представляет опасности для резьбовых соединений.
Мокрая и влажная коррозия — самые опасные виды коррозии для стальных изделий.
При выпадении дождя или росы вода проникает внутрь резьбового соединения под действием капиллярных сил в капиллярах, расположенных между наружной резьбой болта (шпильки) и внутренней резьбой гайки, а также в макро-и микрокапиллярах, образованных шероховатостью поверхностей гайки и зажимаемого ею стального изделия.
При отсутствии дождя и росы, т.е. при относительной влажности воздуха меньше 100%, влага все равно заполняет вышеуказанные капилляры за счет капиллярной конденсации из воздуха, обусловленной зависимостью равновесного давления паров воды от формы поверхности и степени кривизны мениска жидкости в капиллярах. С уменьшением радиуса капилляра уменьшается радиус кривизны вогнутого мениска жидкости, что приводит к росту капиллярной конденсации при постоянной относительной влажности наружного воздуха меньше 100%.
Механизм электрохимической коррозии
Итак, мы установили, что на всех открытых окружающей атмосфере поверхностях резьбового соединения всегда присутствует пленка влаги (видимая или невидимая). В этой пленке постепенно растворяются такие компоненты воздуха, как углекислый газ, оксиды серы и азота. Известно, что при растворении в воде углекислого газа образуется угольная кислота, при растворении оксидов серы и азота — серная и азотная килоты. Что из этого следует? А то, что пленка воды превращается в слабый (очень малая концентрация кислот) электролит, т.е. она проводит электрический ток за счет перемещения электрически заряженных частиц — ионов различных соединений, в том числе ионов металла, на котором находится пленка электролита.
Известно, что у поверхности металла, погруженного в электролит, образуется двойной электрический слой, в результате чего металл приобретает электрический потенциал, т.е. становится электродом. Если бы металл был абсолютно однороден по своим свойствам, то электрический потенциал в каждой точке его поверхности был бы одинаков, а поскольку при отсутствии разности потенциалов электрический ток не появляется, то в этом случае не было бы и электрохимической коррозии. На самом же деле сталь, из которой изготавливаются резьбовые соединения, имеет множество неоднородных включений, которые на границе с электролитом имеют разный электрический потенциал.
Разность потенциалов посторонних включений и неоднородностей самого железа (оно состоит из деформированных кристаллитов, выходящих на поверхность изделия то гранями, то углами) в присутствии пленки электролита приводит к образованию множества макро — и микрогальванических элементов, по которым течет электрический ток — в виде потока электронов в точках контакта частей металла с разными свойствами (аноды и катоды), и в виде движения ионов в пленке электролита. Эти процессы и являются электрохимической основой атмосферной коррозии.
Коррозию стальных резьбовых соединений можно представить в виде следующей упрощенной схемы: электрохимическое растворение железа в электролите путем отрыва положительно заряженных ионов железа от стальной поверхности, взаимодействие этих ионов с отрицательно заряженными гидроксильными остатками диссоциированных молекул воды и с растворенным в электролите кислородом, образование труднорастворимых гидратов закиси и окиси железа, и, наконец, образование сложных гидратированных (т.е. прочно связанных с некоторым числом молекул воды) нерастворимых окислов железа бурого цвета. Этот последний продукт и есть всем известная ржавчина.
Факторы, влияющие на атмосферную коррозию резьбовых соединений
Влажность воздуха является основным фактором, определяющим скорость коррозии. При изменении относительной влажности воздуха от 0 до 60% коррозия изменяется незначительно — от 0 до 5 мг/дм2 (масса ржавчины на единицу поверхности), зато дальнейшее увеличение влажности всего лишь на 5% (до 65%) приводит к резкому скачку коррозии — от 5 до 40 мг/дм2.
Вторым фактором, ускоряющим коррозию, являются частицы пыли, оседающие на резьбовое соединение и увеличивающие капиллярную конденсацию влаги, которая со временем превращается в электролит.
Третьим серьезным фактором является характер атмосферы и географический фактор. Наиболее агрессивной является атмосфера индустриальных районов, наименее агрессивна чистая и сухая атмосфера континентальных регионов.
Защита резьбовых соединений от коррозии
Специфика резьбовых соединений состоит в том, что их более или менее часто приходится разбирать, поэтому практически единственным методом защиты от коррозии в данном случае является смазка резьбового соединения. Однако смазка является временной защитой, поскольку через нее, хотя и медленно, проникают к металлу и пары воды, и кислород. Некоторые из смазок набухают под воздействием атмосферной влаги. Кроме того, сами смазки со временем могут вызывать коррозию, окислившись под влиянием окружающей атмосферы. С целью увеличения защитных свойств смазки, в нее часто вводят ингибиторы (замедлители) коррозии, такие как этаноламины, аминофенол, тиоэфиры, кетоны и др. Большинство из этих соединений растворимы в воде. Конкретный пример эффективного ингибитора — карбонат моноэтаноламина.
Ингибиторы коррозии плохо вводятся в смазки, поэтому их диспергируют в смазке с помощью специальных гидродинамических эмульгаторов, добавляя небольшое количество мыла для стабилизации эмульсии.
Как разобрать, как очистить от ржавчины резьбовое соединение
Мы уже выяснили, что ржавчина представляет собой комплексное химическое соединение, состоящее из оксидов железа, гидратированных молекулами присоединенной воды. Так как молекулы воды ослабляют связи между молекулами окислов, ржавчина является сравнительно непрочным соединением, однако прочности ее иногда хватает, чтобы не дать вам открутить заржавевшую гайку.
Как решить эту проблему? Очень просто. Мы знаем, что ржавчина является пористым гигроскопичным веществом. С другой стороны известно, что смачивающая капилляры жидкость обладает расклинивающим действием в узких капиллярах, частично разрушая структуру и уменьшая прочность пористого тела. Отсюда решение — приготовить мыльный раствор (мыло вводится для улучшения смачиваемости пор) и замочить в нем на 1-2 часа резьбовое соединение, периодически его обстукивая. Это приводит к проникновению жидкости в самые тонкие трещины и поры, ослабляя прочность ржавчины. Вместо мыльного раствора можно использовать керосин, но для этого нужно тщательно высушить резьбовое соединение. Как известно, керосин очень хорошо смачивает сухие металлы (его используют для проверки сварных швов) и обладает высокой расклинивающей способностью в тонких порах. Разобрать резьбовое соединение с полуразрушенной ржавчиной уже не представляет большого труда.
Ржавчину можно сравнительно легко удалить минеральными кислотами — серной, соляной, азотной. Однако кислоты, растворяя ржавчину, разрушают и поверхность металла, делая ее в дальнейшем легкоуязвимой для коррозии. Добавление к кислоте указанных выше ингибиторов коррозии замедляет растворение в ней металла, не замедляя в то же время растворения ржавчины. Этим способом можно удалить ржавчину из резьбового соединения, не нарушая целостности резьбы.
Время, необходимое для удаления ржавчины, зависит, в основном, от шероховатости металла и для обычной неполированной поверхности при использовании 20%-й кислоты составляет 1,5 — 2 часа. Обработка резьбовых соединений кислотами, содержащими ингибитор, производится в эмалированной ванне, а если это по каким-то причинам невозможно, на очищаемый узел накладывают тряпки, смоченные в кислоте с ингибитором.